Chemical Logistics: Increasing Safety and Effectiveness with a 3PL
You see flashing lights up ahead. Almost immediately they are accompanied by brake lights, yours included. After a few minutes of idling, you tune in for a traffic report and learn that this is not a typical fender bender. Instead, a tanker truck is leaking a corrosive and reactive substance. As fire trucks and other first responders begin to speed by toward the scene, your inconvenient stay in traffic just became a frightening ordeal.
This is a scary scenario, not only for the general public, but for chemical manufacturers everywhere. When it comes to chemical logistics, there are some additional complexities and unique priorities involved. Transporting, storing and distributing flammable and hazardous materials can have significant environmental and financial consequences. The chemical industry touches every part of our lives from petroleum and natural gas refining to developing additives and synthetic materials. According to the American Chemistry Council’s 2013 Chemical Industry Situation and Outlook, by 2018 the U.S. chemical industry will reach $1 trillion in sales.
With such tremendous volume, the chemical industry’s supply chain has an immense need for scalability and flexibility. As changes in federal and state regulations become more complex and stringent, the challenges that face supply chains in other industries become magnified. The United States’ chemical output is expected to increase by 2.5% this year, and 3.5% next year. With a forecasted annual growth rate of over 4% through the end of this decade, the chemical industry will outpace the overall U.S. economy.
While the outlook is certainly bright, and the economic indicators are optimistic, chemical producers must make wise decisions and remain diligent in their logistics operations and management. Safety is a key consideration for all industries, especially chemical manufacturers who must place it above all else, even cost. Executing safe and effective transportation, storage and handling is a critical asset. As this industry continues to expand, the feasibility of maintaining these safety standards will become more difficult. A direct result of this will be the utilization of third party logistics, or 3PLs.
Here is a list of what you should keep in mind evaluating a 3PL.
- Check maintenance defects and accident records.
- Analyze drive logs.
- Review equipment maintenance logs.
- Verify technological capabilities by requesting a demo.
- Ask for industry references and a few names of current customers.
- Check that the 3PL has the proper certifications and licenses to handle your goods.
- CFATS (Chemical Facility Anti-Terrorism Standards) compliant facilities offer features and standards that adhere to the Department of Homeland Security. These performance based standards bolster the security efforts of your company.
With promising growth on the horizon and new developments being made each day, the chemical industry is major factor in the national economy. With that being said, the safety protocols and processes for chemical logistics have never been more important. With major economic and ecological consequences around each corner, leveraging the expertise of a 3PL can take a major burden away from chemical manufacturers. At Barrett Distribution Centers, the resources and knowledge are available to safely and securely manage the chemical supply chain. With a CFATS facility, safety equipment and experienced personnel in place, Barrett Distribution cannot only improve your logistics, but your overall business.
Recent Blog Posts
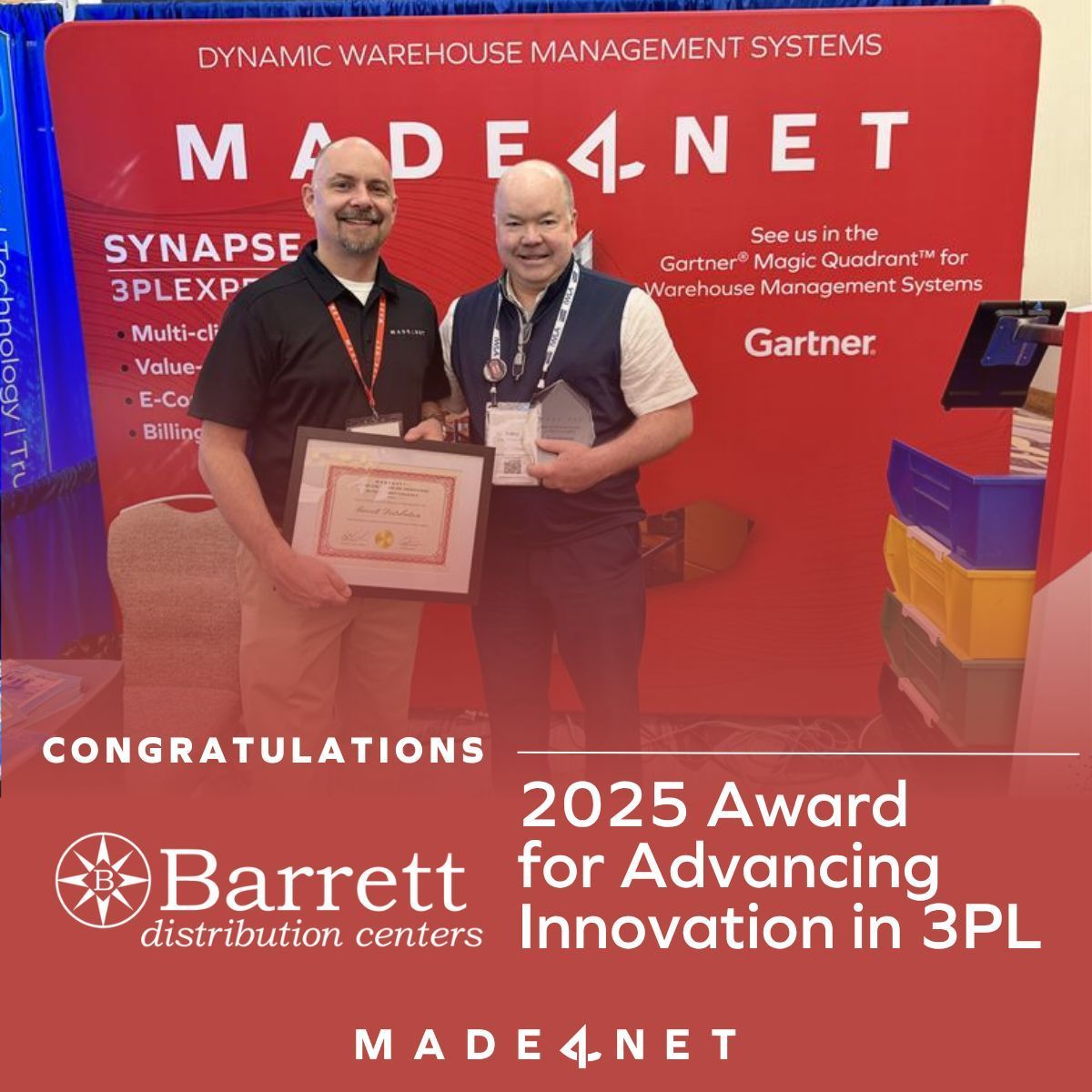
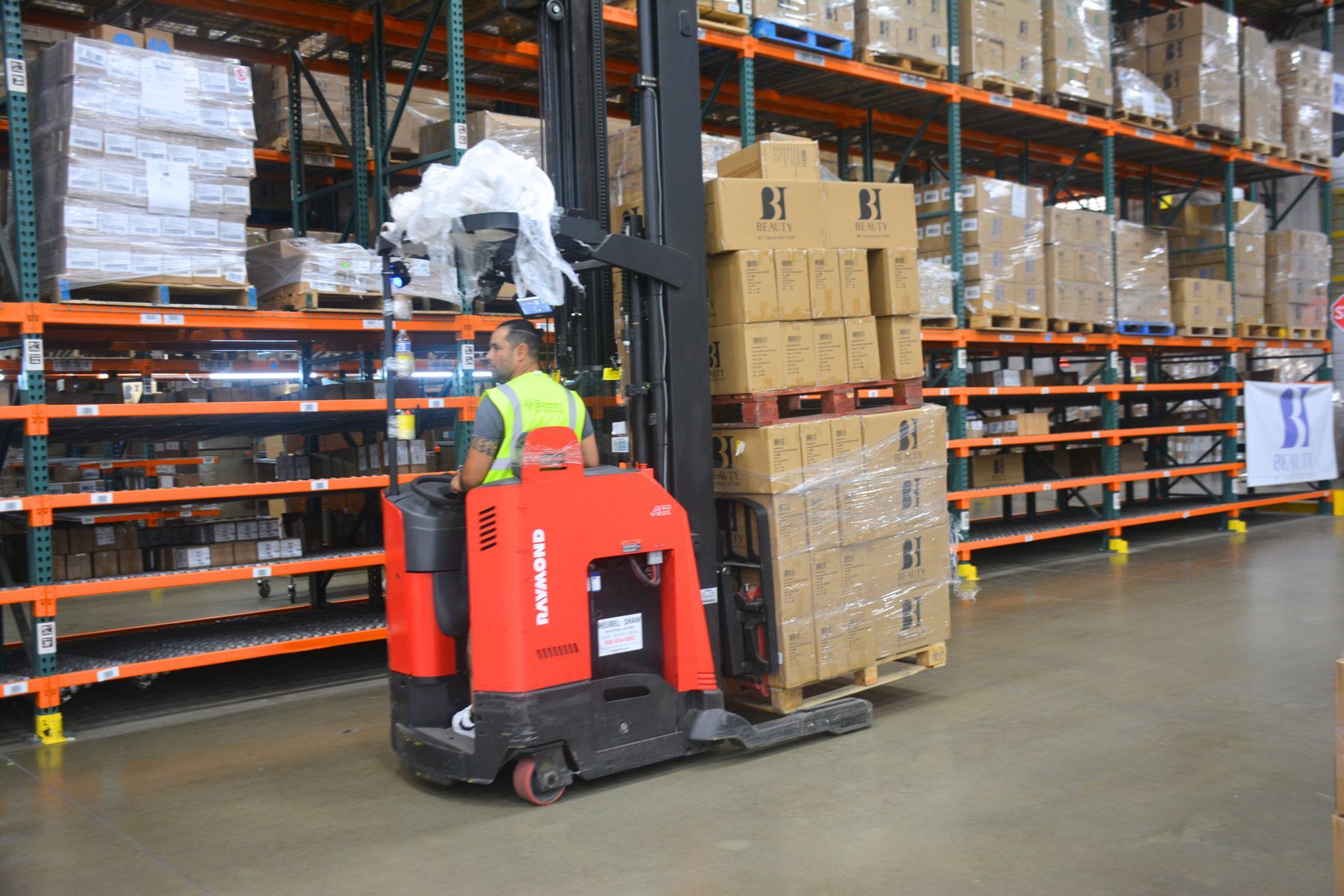
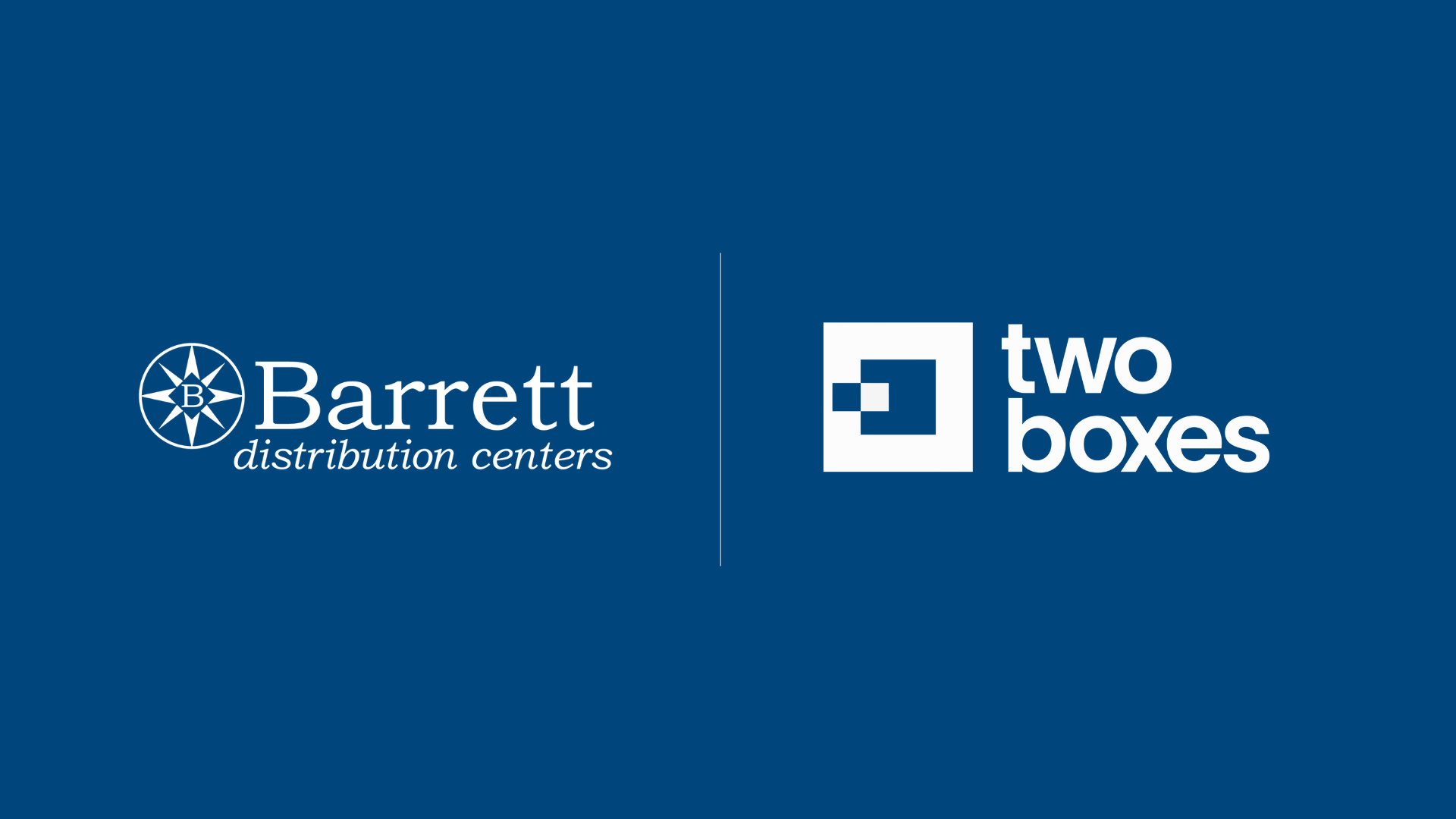